MVP Lab Report – July 2025
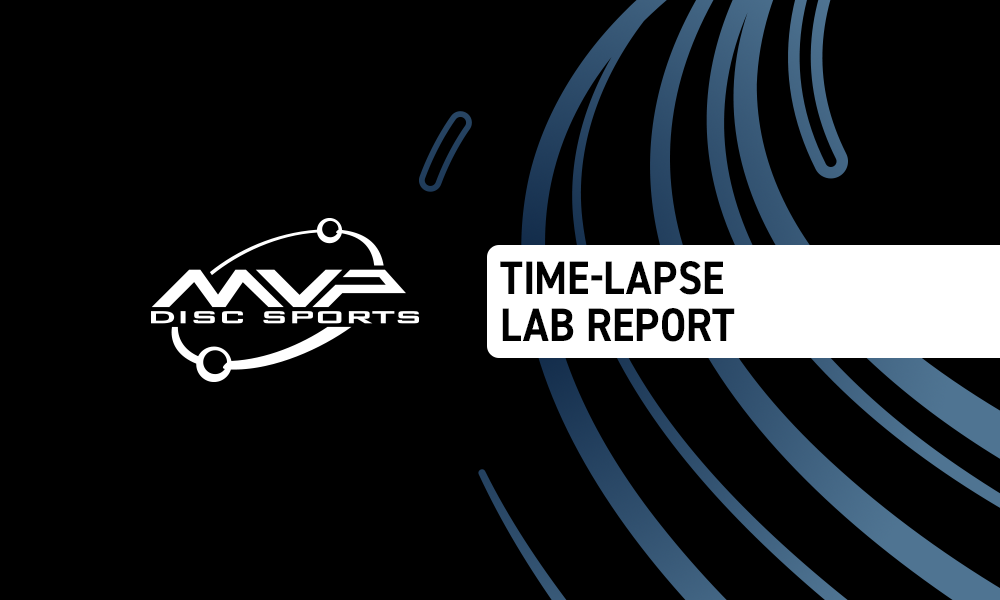
With Simon’s most recent vlog, the news is finally out: we are retooling the Time-Lapse. As the first ever disc in the Simon Line and MVP’s first 12-speed distance driver, the Time-Lapse was poised to be one of MVP’s biggest hits. However, there was an issue – the process of developing the perfect 12-speed distance driver has been far more difficult than expected, and some valuable lessons ensued during the process.
Our goal for the Time-Lapse was to create a distance driver that high-power players would trust for controllable maximum distance, and lower-power players would appreciate for reliable and predictable flights. The initial Prototypes, as seen in Simon’s Time-Lapse reveal vlog, were just that. Simon was ecstatic, and MVP was excited to make this come to life. We knew we had something special on our hands.
However, as reports of the First Prototype Run started coming in, we started to learn that this run of prototypes was not flying consistently with the original prototypes that Simon had tested and approved. We quickly started making adjustments as we went into the First Production Run to better replicate the original prototypes that were perfect for Simon. We persistently monitored the dimensions of the production run to ensure they matched what Simon was hoping for. Everything checked out dimensionally as the production run progressed. Unfortunately, the first release still missed the mark on intended stability. We recognize this may have left some early adopters of the Time-Lapse feeling disappointed, and we genuinely share that disappointment. While the more overstable Production Run Time-Lapse were still good discs, they weren’t the disc Simon and MVP set out to make together. That disappointment motivated us to deeply examine what happened, refine our processes, and commit ourselves even further to deliver an improved Time-Lapse.
We started comparing the original prototypes with the first production run, both visually and comparatively in flight. As we scrutinized the original prototypes with the production run, it was clear that there were some very fine differences between the two. However, as far as we could measure, they were seemingly consistent in measurement. This was when it started to dawn on us that the measurement tolerances required for high-speed distance drivers were far tighter than what our current measurement method could muster. This was despite the fact we were using a high-precision marble slab, a Mitutoyo height gauge, 10X optics, and overhead lighting.
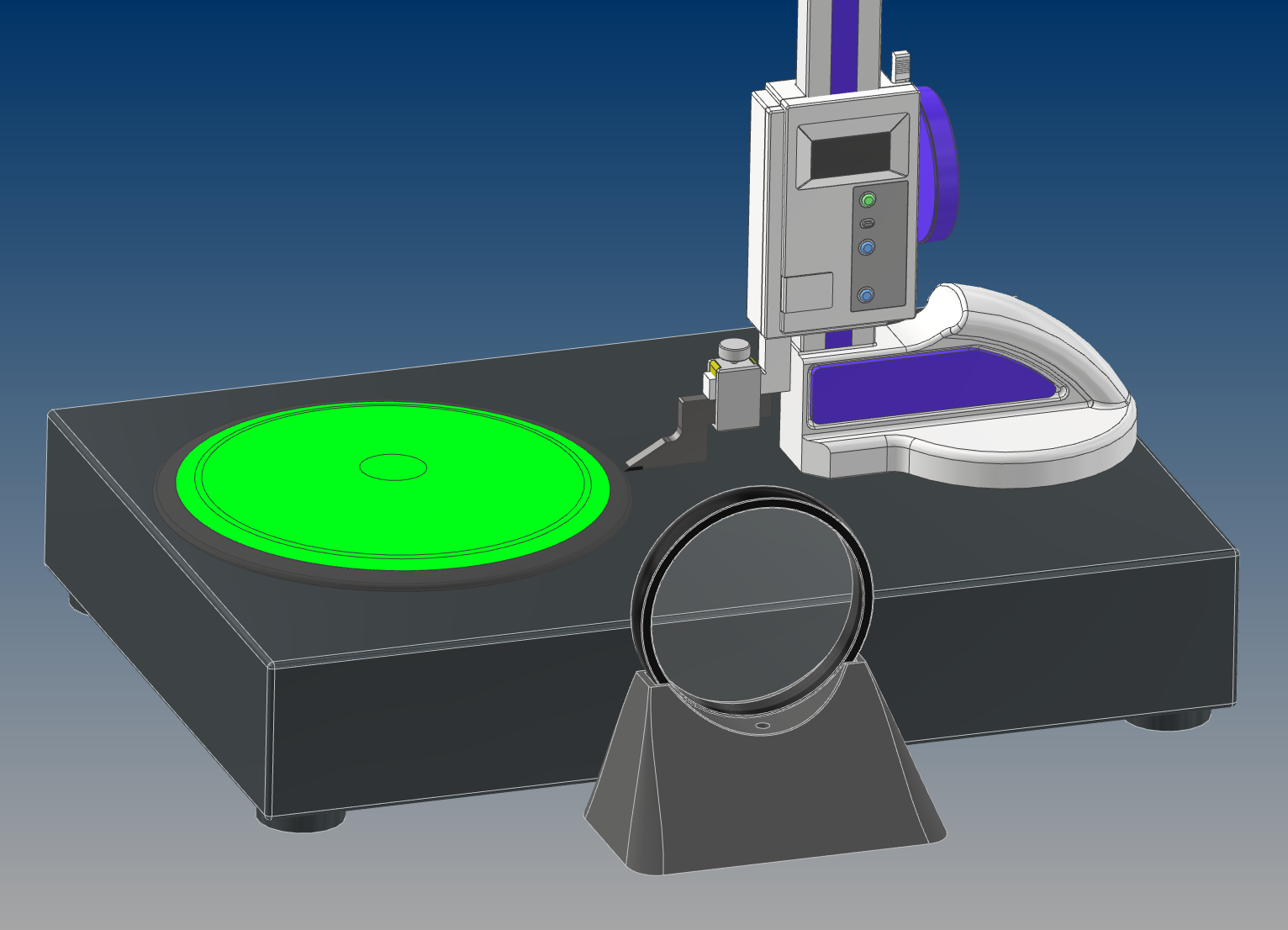
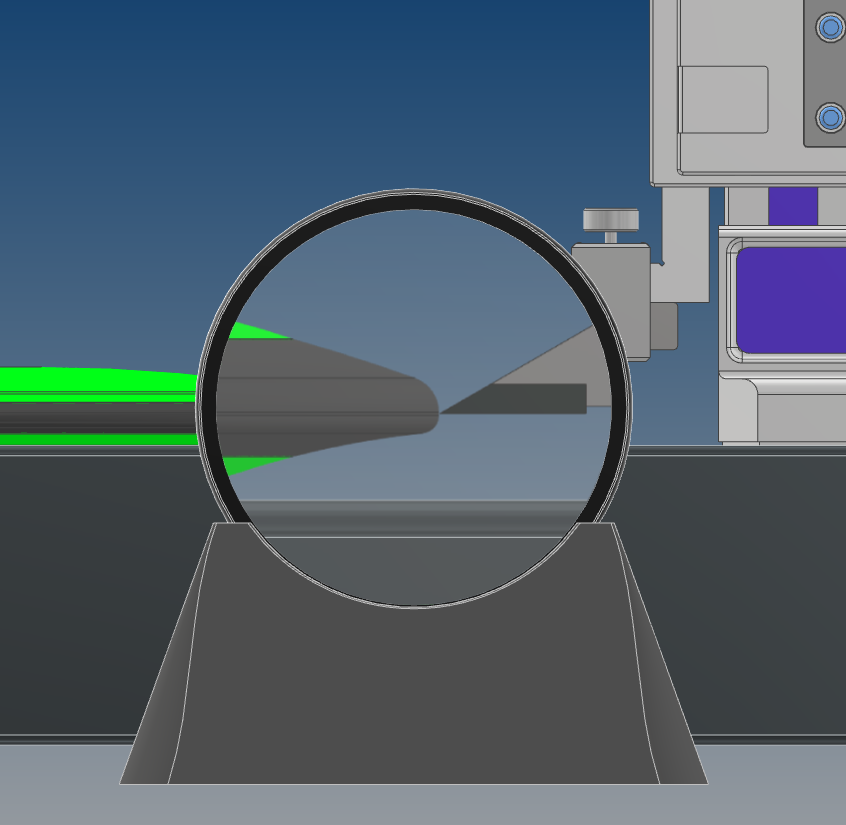
These are industry-standard quality measuring tools capable of extremely high accuracy. Where the first challenge arises is that the object that we are trying to measure (i.e., Parting Line Height flash) is as thick as 0.8-1.0mm. When we implemented this measurement process, we recognized that our quality team could either measure the top of this feature, the bottom of this feature, or “the middle” of this feature. We opted for measuring the “middle” of this feature. Unfortunately, however, obtaining accurate measurements of this feature isn’t that simple. This PLH “flash” is variable as you rotate the disc on a flat surface. In other words, this flash is varying in height AND thickness as the disc is rotated, especially to an extent that is greater than what is required for accurately measuring PLH to the accuracy that is required for a consistent flying golf disc. Essentially, trying to measure the PLH is literally trying to hit a moving target with a bullseye that is changing size.
Enter the new measurement method. Within the same month of the First Run Time-Lapse (November 2023), we invested in a Keyence Laser Microscope, a $50K piece of equipment capable of measuring with sub-micron tolerances. This equipment can much more accurately measure the PLH by profiling the nose and taking the true geometric centerpoint of the nose profile. You can see this equipment demonstrated on the Smarter Every Day 2 YouTube Channel. We were on our way to achieving perfect consistency now that we have the proper equipment that’s going to enable us to achieve the dimensional consistency necessary for making the perfect high-speed distance driver, right? Still not quite…
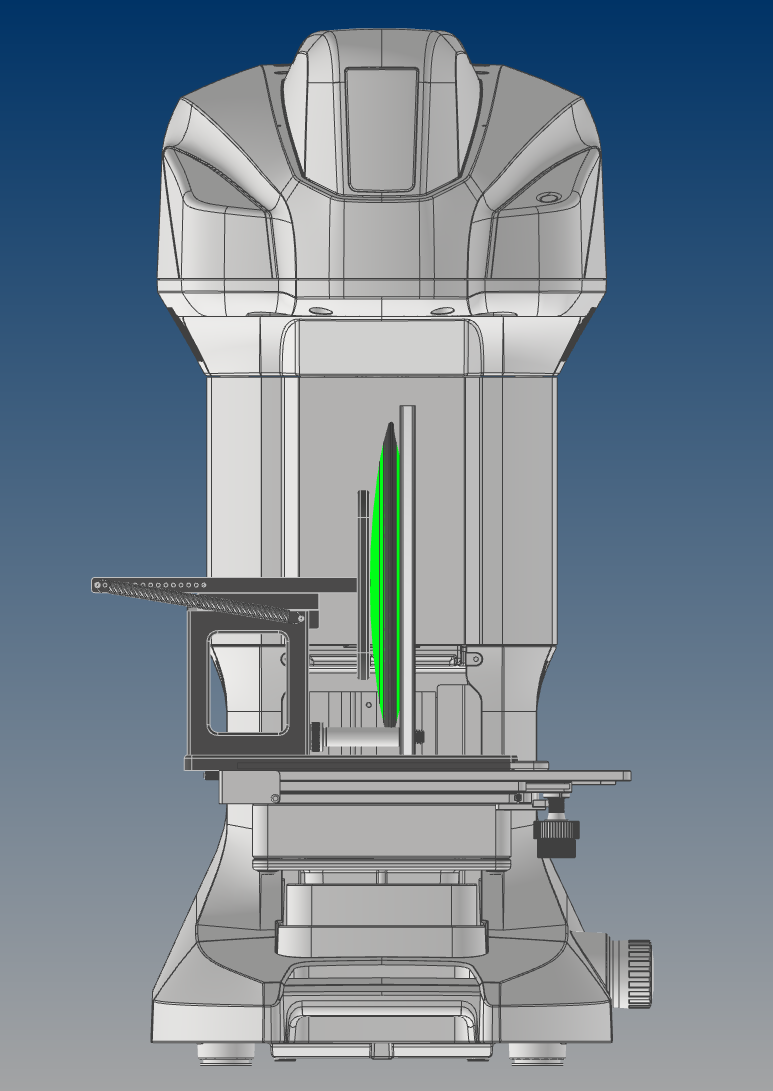
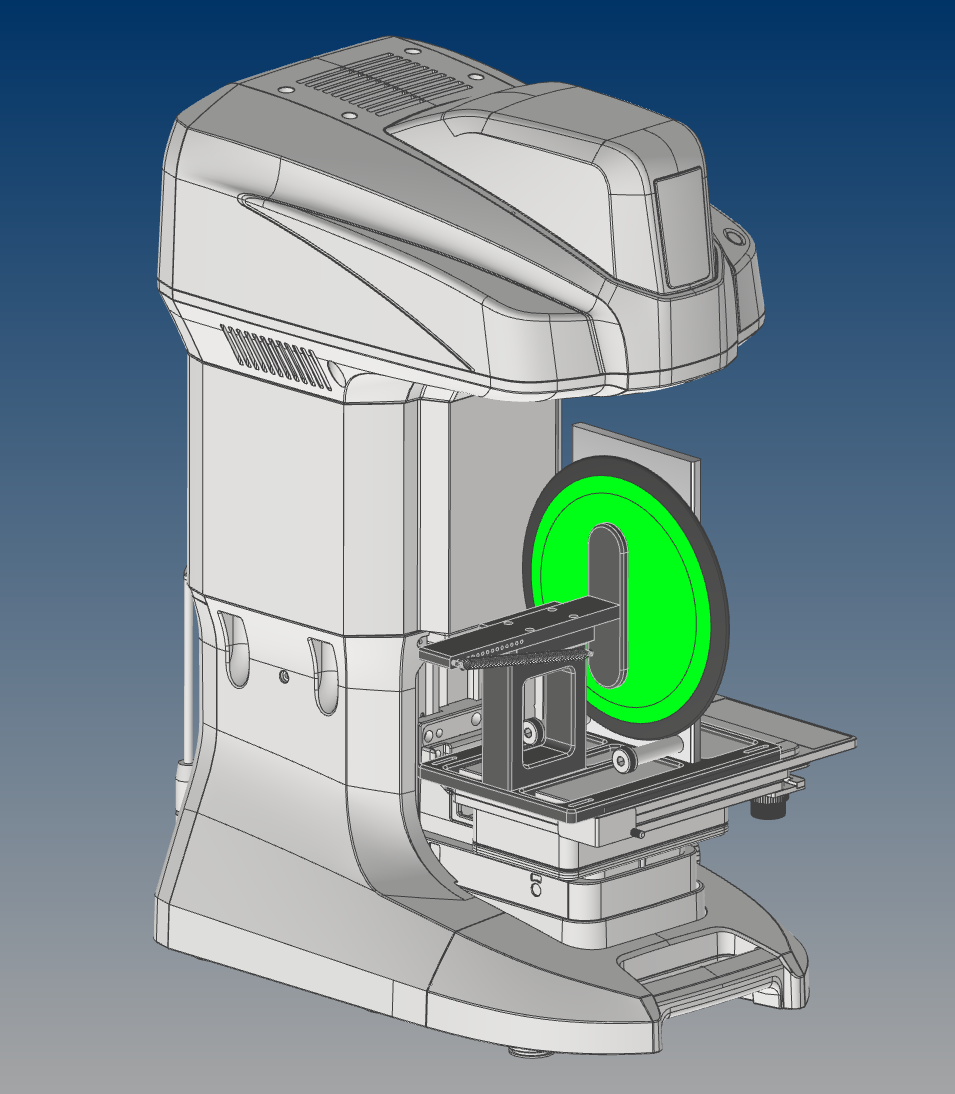
While this new equipment has enabled us to significantly improve the measurement accuracy required for disc golf discs, this is where we further learned how challenging it really is to make highly consistent golf discs.
Enter Melt Flow Index. Essentially, this is a property that correlates with the viscosity of the plastic in its molten state by measuring how it flows under standardized conditions, including the defined chamber orifice size, chamber temperature, applied weight on the plunger, and time. This property impacts how the molten plastic flows into the mold during the injection process and therefore dictates the process conditions required to make an acceptable quality disc, cosmetically. However, these varying process variables will inherently lead to inconsistent results dimensionally once the plastic shrinks and cools coming out of the mold. Also featured in the Smarter Every Day 2 YouTube Channel is the Melt Flow Index Analyzer equipment in our quality lab, which demonstrates how vastly the Melt Flow property of our plastics can vary, despite being the same grade of material from the same supplier. This challenge is at the heart of the consistency issues faced by every disc golf manufacturer, and to our knowledge, no company has fully overcome it.
Even the colorant pigments used significantly impact the Melt Flow Index during the injection process. We have since migrated our color-dosing methods to a new fully-custom in-house designed system that enables us to dose different colors more consistently. Even with this system, which represents a vast improvement over traditional color dosing solutions in the plastics industry, factors outside of our control, such as the shape of the pellet, can result in inconsistent color dosing. It only takes the difference of a few pebbles dosed in a cycle to result in a vastly different disc dimensionally.
After learning about the severity of impact of this property, we have since implemented stricter MFI tolerances than the standard tolerances set forth by our plastic supplier. They have graciously worked with us to further narrow down the MFI tolerances required for our golf discs. In fact, this is the first time they have seen an application that has required MFI tolerances this strict for TPU plastics (comparatively, other TPU applications, such as caster wheels, cabling, etc., have not required MFI tolerances of this extreme).
While we have greatly narrowed the tolerances at the source (i.e., the raw plastics and the color-dosing process), the range of MFI on our supply of plastics still remains problematic. We expect significant improvement from the variance that has been observed in recent runs, such as the Time-Lapse and Trail, but consistency still remains imperfect. This doesn’t mean that we have abandoned our efforts. In fact, we have only since doubled down on our efforts to overcome this challenge, as we believe the importance of consistency is worth it. Our effort to continuously improve our process and consistency will always be a top priority for us.
Our ever-improving processes and quality control have driven us to overhaul our internal R&D qualification process so that we aim to deliver a product that hits the stability targets that we are aiming for.
Circling back to the Time-Lapse Retool project, after having spent over a year trying to refine the process to replicate the original Prototype Time-Lapse, we have found that it was not feasible to do so. This was heartbreaking, internally. We had made the perfect prototype but were unable to replicate it under the conditions required for reliable production. However, it led us back to the drawing board with much greater knowledge. We met with Simon to have an extensive discussion about how the Time-Lapse was molding up and where we wanted to take it from here. Simultaneously, Simon’s time with the original Time-Lapse allowed him to hone in on fine details about how it felt in the hands, particularly with the shoulder angle. The adjustment to the shoulder angle was extremely small (less than 2 degrees), but the impact on the comfort of hand feel was substantial. More importantly, however, the new Retooled Time-Lapse flies as intended. In conjunction with this shoulder angle adjustment were some very fine adjustments to PLH on the order of literal hair-splitting adjustments (+/- 100 Microns). Adjustments of this fineness are what separated the V2 and V3 as demonstrated in Simon’s Retooled Time-Lapse Vlog. Going through the process of retooling Time-Lapse with building 2nd and 3rd versions of new molds simultaneously, while extremely costly, was well worth it – we finally have the Time-Lapse that we have been looking for.
With everything that we have been through during this journey, we have become a much better company. We’re extremely excited about what we have learned throughout this journey and what it’s going to lead us to in our future development. To all the players who’ve patiently stuck with us through this journey, your feedback, trust, and support have made all the difference. We can’t thank you enough for helping us grow and continually improve.
We can’t wait for you to throw this new Time-Lapse, and show you what the future holds!
Sincerely,
Brad Richardson
MVP Disc Sports